Health and Safety in the Infrastructure Industry: What's Required?
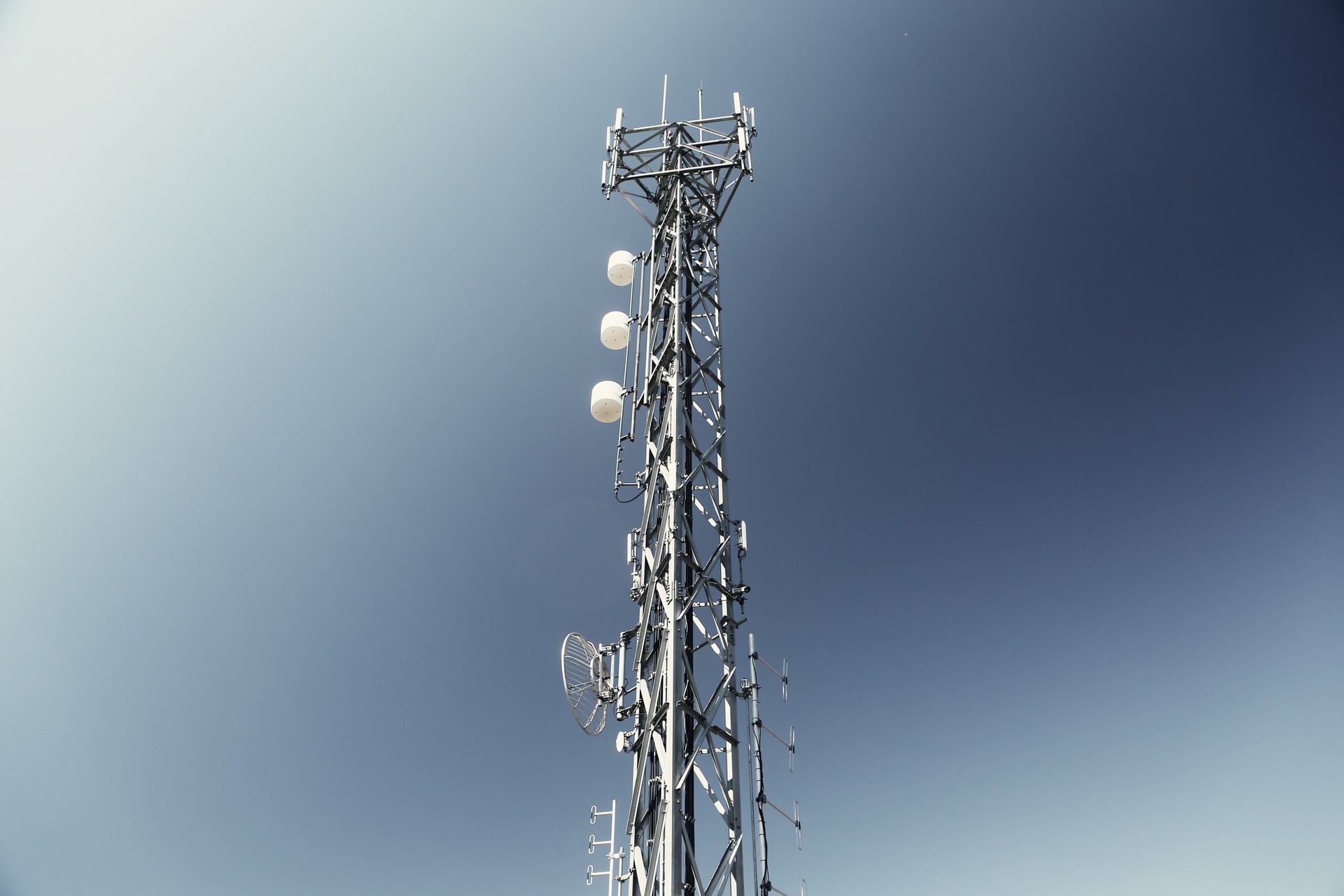
A former government adviser warned the construction industry that health and safety is a “ticking timebomb”, as a result of HSE budget cuts.
The construction industry has been hiring in record numbers in recent years, thanks to a new post-recession boom in property and infrastructure projects. The tragic downside of this is the number of industrial incidents in building sites has doubled in recent years. Between 2001 and 2014 there have been 760 deaths on building and infrastructure sites.
One Death Too Many
Baroness Donaghy warned of this in One Death Too Many, a landmark report prepared for the last Labour government. A construction boom, coupled with inexperienced new recruiters and safety budget cuts is leading to the situation Donaghy predicted. The 2010 report was praised by the government at the time, only to be ignored by successive Coalition governments.
Since then, HSE funding has been cut 35% in 2011, as a response to austerity measures. The construction workers’ union, Ucatt, informed The Guardian that there was a reduction in unannounced inspections, improvement notices and prosecutions for safety violations between 2011-14.
As Donaghy warned, “there is a danger that skills have been lost during the recession, and people who are insufficiently skilled will be taken on. And that’s when the deaths and accidents will start taking place.” HSE budget cuts clearly won’t help reduce the risk of a rise in workplace deaths and accidents.
General secretary of Ucatt, Steve Murphy said in an interview: “I sincerely believe the construction industry is chaotic. And deaths on sites will tragically rise in the next year.”
How can managers prevent tragedy?
The sad fact is that not all – not 100% – of accidents can be legislated against, but tragedies such as these are preventable. So are deaths caused by negligence or inexperienced workers not fully understanding the risks or appreciating the precautions they need to take on infrastructure sites.
Construction and infrastructure projects fall within a wide range of laws and guidelines designed to protect workers, the general public – where applicable – and contractors.
Here are a few of the most commonly applicable laws:
- The Construction (Design and Management) Regulations 2015 (CDM 2015)
- The Work at Height Regulations 2005
- Provision and Use of Work Equipment Regulations 1998 (PUWER)
- The Lifting Operations and Lifting Equipment Regulations 1998 (LOLER)
- Health and Safety at Work etc. Act 1974 (HSWA 1974)
- The Personal Protective Equipment Regulations 2002
With each, we have already covered how the laws apply in practice in other articles, or will be writing a complete guide in the coming weeks (we will update this article with new information accordingly).
Managers need a solid, practical understanding of the law, but more importantly, how the relevant laws are applied on their infrastructure site, with their team. The HSE published a book in 1996, with a 2006 update, which has sold over 250,000 copies. At 141 pages it contains, as far as possible, guidelines on how to manage and prevent the most common risks on a construction site.
Construction Site Dangers
It should go without saying, but anyone familiar with building projects knows there’s a higher concentration of dangers than perhaps any other working environment. Most other workplaces are static. They rarely change. Infrastructure sites change all of the time, which when we factor in the weather makes accidental death and injury more likely. The most common cause of accidents are:
- Falls
- Mobile construction plant/machinery – moving vehicles, poor visibility, especially when reversing, or the risk that drivers and operators can be killed or injured if machinery overturns.
- Collapsing materials, scaffolding and building structures.
- Electrical accidents.
- Trips: Over 1000 serious incidents occur every year. Most can be easily prevented.
- Asbestos.
- Manual handling. Often repeated lifting of heavy/difficult loads can cause long-term injuries.
- Noise and vibrations can cause hearing loss and harm to the hands and fingers, from repeated use of vibrating tools (hand-arm vibration syndrome).
- Chemicals. Exposure to segments and solvents can cause skin conditions. More careful use of PPE can help reduce the risk of harmful exposure.
Managing Risks in Infrastructure
Ensuring health and safety is managed carefully on a construction site involves the following:
- Planning
Effective health and safety begins with the planning stage. Ensuring everyone is safe means working through the following checklist at each stage of the project: plan, organise, control, monitor and review. When it comes to building sites, this isn’t only a job for those with ‘health and safety’ in their titles; it’s everyone’s responsibility.
Planning should involve gathering as much information as possible about the project, the site, materials being used, storage, deliveries, scaffolding, skills required, and the cost of safeguarding/reducing risks.
Only when a construction project is going to take more than 30 days, or involve more than 500 person days of work should the HSE be notified in writing.
- Setting up the site
Before work can start, the site must be made ready for construction crews. This can take a few days to a few weeks, depending on the size of the project.
Safety is one, key consideration, but adequate rest, toilet, storage and other facilities must be established. Once you have more than 5 staff/contractors, there must be at least one first aider, with an additional once you have more than 50 people on the site. Emergency exit routes and fire evacuation points must be set up, along with adequate and safe access routes, lighting, scaffolding and boundaries.
It’s crucial that everyone is trained on relevant safety procedures and site rules, including clients, who will need separate rules for when they’re on site.
- Work in progress
- Risk assessments need to be ongoing, for each new phase of work. The aim should always be, as far as possible, to eliminate a risk. When that can’t be done, it must be reduced and mitigated, to ensure the duration and number of workers exposed to any risk are reduced, as far as possible.
- Once action is agreed, those responsible need to ensure this is done, which includes, ensuring:
- Everyone – staff and contractors – are properly trained and competent;
- They have all the necessary equipment / PPE as required;
- Safer working methods are put in place;
- Accidents, injuries and near-miss incidents are reported up the management chain, including between contractors, subcontractors and the client. Supervisors should always be informed, especially when an incident almost happens, to find ways to avoid similar dangers in the future.
- HSE inspections can happen, which is something no supervisor should worry about if safety measures are effective and being monitored.
Managing health and safety on a infrastructural site isn’t easy. With Papertrail, you get a complete safety management system to help you stay in control of risks, paperwork, equipment, record keeping and inspections. Book Your Free Demo today!
Improve your inspection management system today
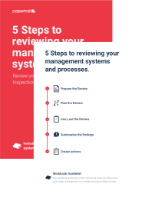