5 Safety Regulations You Need to Know
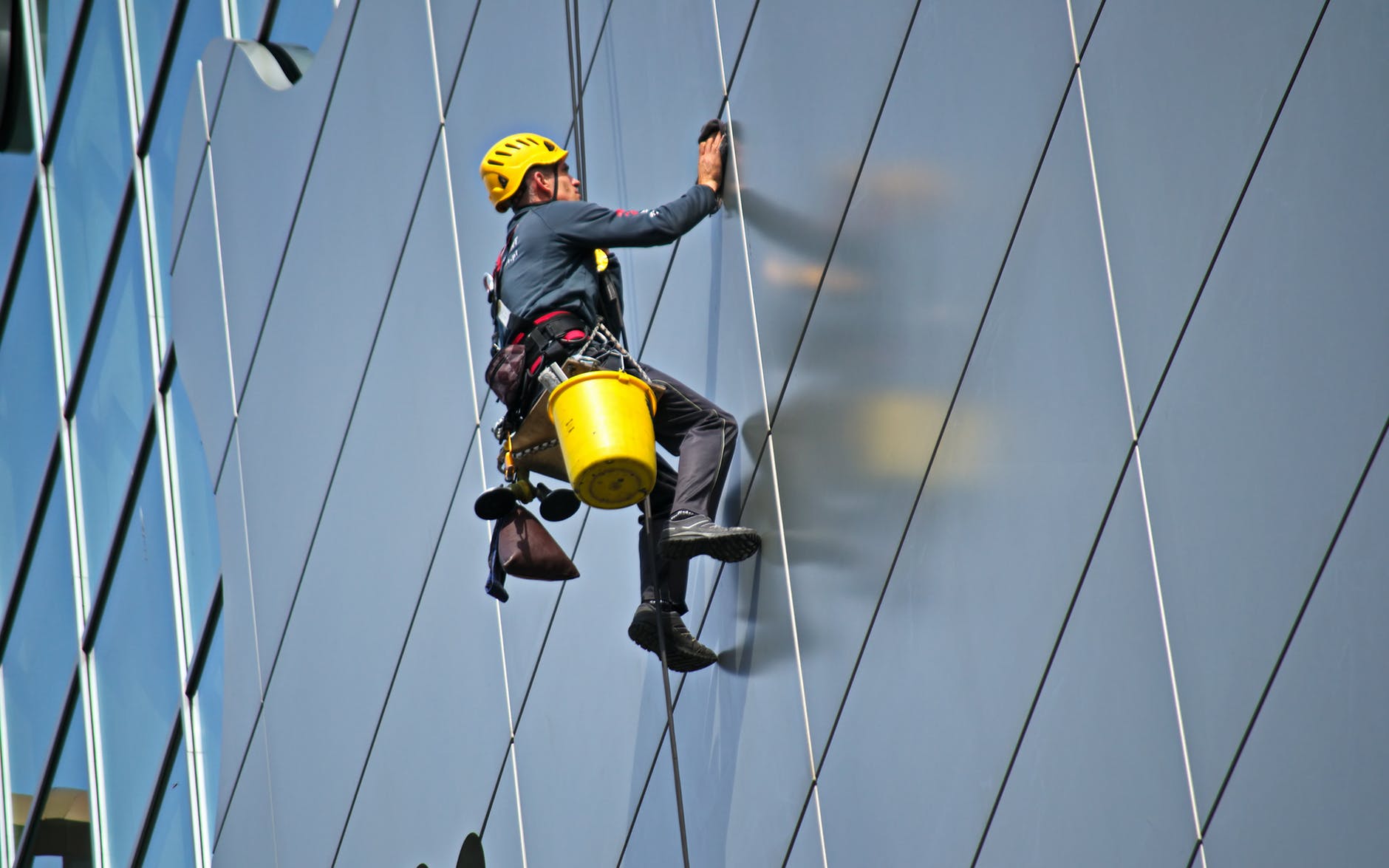
Why you must inspect equipment and keep records
As an Equipment Manager, it is necessary to inspect any equipment where there could be risks to health and safety. A risk assessment should be carried out to determine if there is any need for inspections and routine maintenance to ensure the continued safety of your colleagues. Inspections must be recorded and evidenced, a management system like Papertrail can help you complete inspections in a clear, efficient and systematic way.
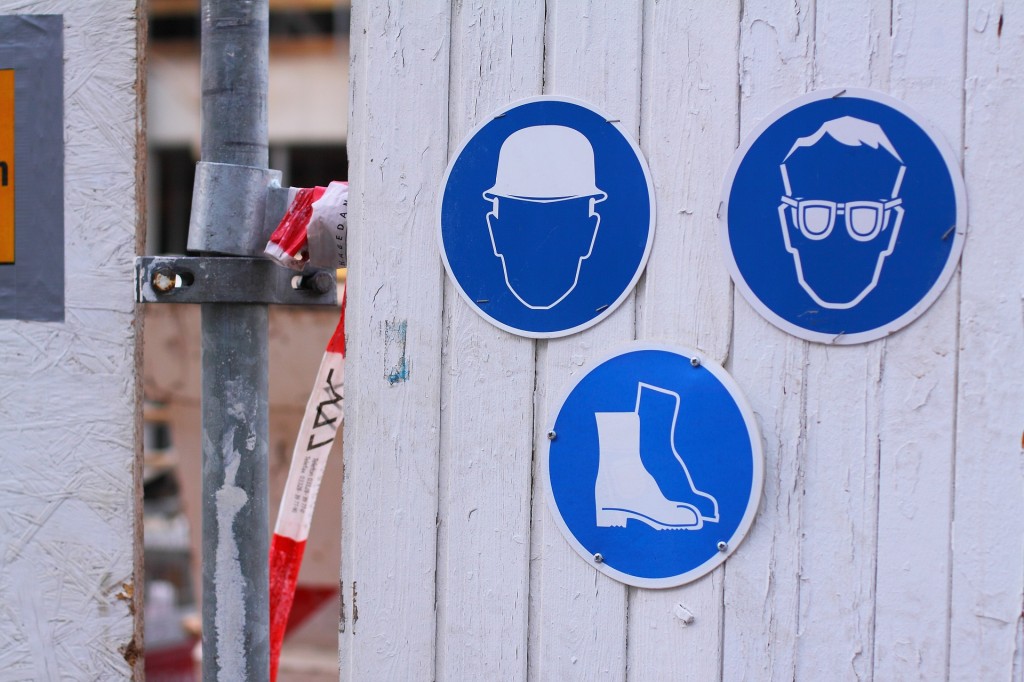
Regulations to be aware of
There are five main regulations that businesses with safety equipment must consider:
- The Health and Safety at Work Act 1974
- The Personal Protective Equipment At Work Regulations 1992
- PUWER
- LOLER (if you’re using lifting equipment)
- WAHR (if you’re working at height)
1. The Health and Safety at Work Act 1974
The Health and Safety at Work Act 1974 (HSWA, the HSW Act, the 1974 Act or HASAWA) is the main piece of legislation covering occupational health and safety in the UK. The act clarifies the general responsibilities of everyone from employers and employees to owners and managers of the workplace for maintaining health and safety.
2. The Personal Protective Equipment at Work Regulations 1992
The Personal Protective Equipment At Work Regulations 1992 is a set of regulations created under The Health and Safety Act placing liability on the employer to ensure suitable personal protective equipment has been granted for those who may be exposed to a risk to their health or safety at work.
3. Provision and Use of Work Equipment Regulations 1998 (PUWER)
These regulations aim to make work safer for anyone using and coming in contact with equipment, this includes employers, employees, contractors, suppliers and people who may need to access any equipment. The regulation ensures that equipment is kept in good order and that maintenance, training and inspections are carried out to suitable and sufficient levels to identify if the equipment can be used.
4. Lifting Operations and Lifting Equipment Regulations 1998 (LOLER)
LOLER places responsibilities on people and companies who own, operate or have control over lifting equipment. If any lifting equipment is provided you must manage and control the risks to avoid any injuries or damages.
5. The Work at Height Regulations (WAHR)
Falls from height is one of the biggest causes of deaths and major injuries for the work at height sector. The Work at Height Regulations was introduced to prevent death and injury caused by a fall from height.
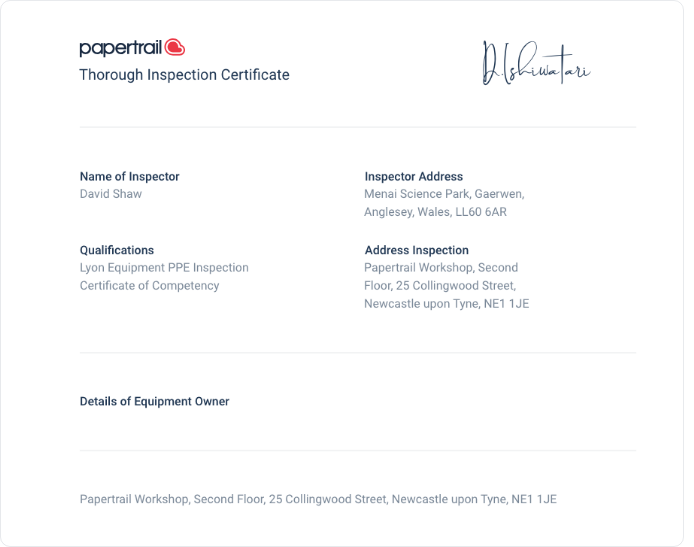
Are you complying with these regulations?
Papertrail helps businesses to comply with health and safety regulations, as well as saving time on inspections and reduce risk.
Using Papertrail allows you to inspect several items and add inspections to multiple records at once, this saves you more time in comparison to logging inspection records individually. Read more on the features of Papertrail that can help you complete inspections and keep accurate records.
You can review and improve your equipment management system today for FREE – created for Equipment Managers.
Download our 5 Step Management System Review Workbook and discover how Papertrail can meet your safety management needs.
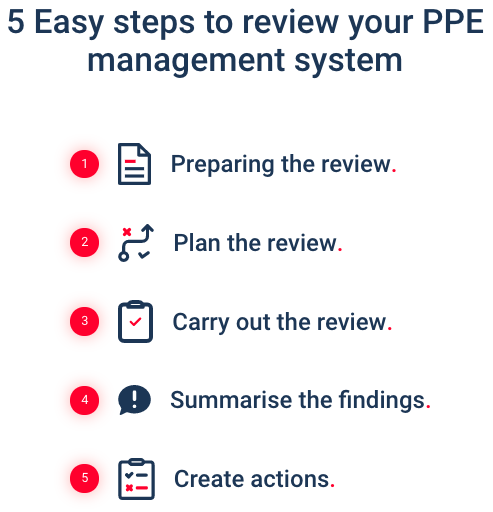
Improve your inspection management system today
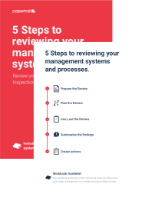